In today’s demanding manufacturing landscape, particularly in sectors such as aerospace, power generation, precision gear and bearing manufacturing and heavy engineering, the pursuit of exceptional precision, efficiency, and cost-effectiveness is paramount.
Production and process engineers are constantly seeking machine tools that not only meet stringent accuracy requirements but also streamline operations and reduce the overall cost of ownership.
RK International Machine Tools, a family-owned company with a history dating back to 1951, has been involved in supplying quality new and used machine tools for many years. When combined with over 30 years of expertise in providing and supporting high-precision grinding equipment, and drawing on this extensive experience, the company says it is proud to highlight the significant capabilities and advantages offered by the Dawn DN Vertical Spindle Series of grinding machines.
Simon Rood, director and general manager at RK International Machine Tools comments: “Vertical grinding technology represents a fundamental shift in how we approach precision grinding, particularly for complex and heavy components. The Dawn DN Series embodies these advantages, offering a comprehensive solution for manufacturers looking to elevate their grinding processes.”
The vertical advantage
While horizontal universal grinding machines have been a staple in workshops for decades, vertical grinding machines, especially those equipped with modern features like Automatic Tool Changers (ATC), offer distinct advantages that directly address many traditional limitations.
One of the primary limitations of many horizontal universal machines is their design focus on “between-centre grinding,” which can lead to interference issues, particularly when handling chucking work. Moving or removing components like the headstock or tailstock might be required for internal grinding operations.
In contrast, vertical grinding machines provide unfettered access for every wheel to the workpiece and dressing device, eliminating the interference issues typically associated with horizontal machines. This inherent design also means precision axes and spindles are positioned up and away from the contamination zone, unlike horizontal machines where they are often located within the coolant contamination area.
This design choice enables vertical grinders to maintain their original performance and accuracy for extended periods, requiring significantly less maintenance, which in turn leads to lower maintenance costs and increased spindle uptime.
“This reduced cost of ownership is a critical factor for any production environment,” asserts Mr Rood.
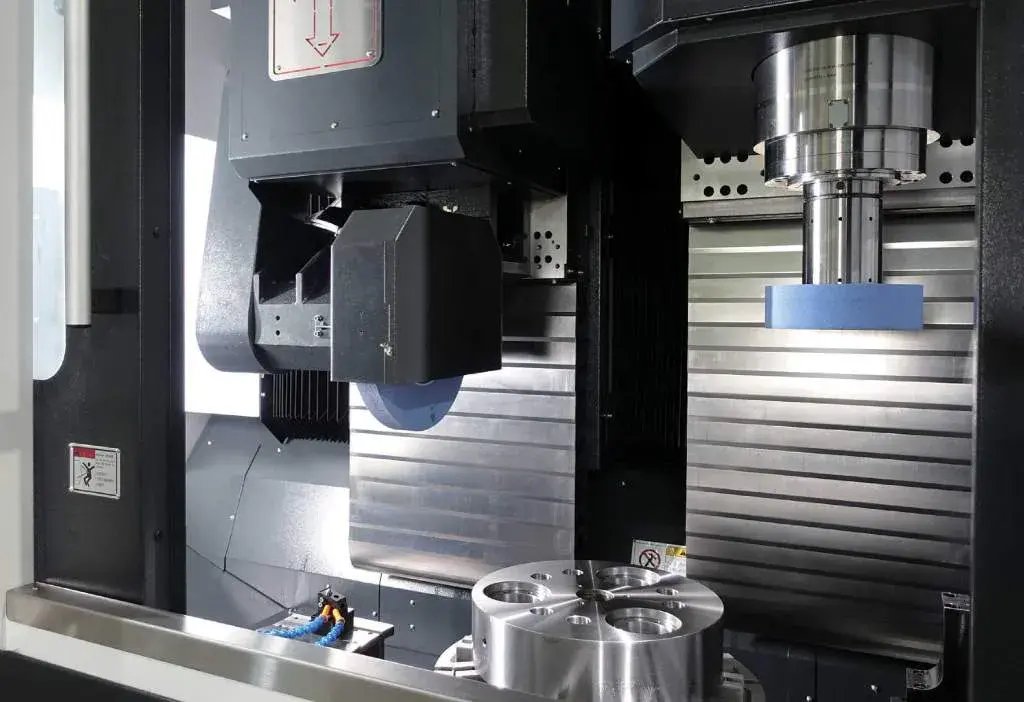
ATC advantages
A key feature available on vertical cylindrical grinders like the Dawn DN Series, which is often not available on most horizontal universal machines, is the integrated automatic tool changer (ATC). The Dawn DN series offers ATC as an optional accessory. This allows for the use of multiple grinding wheels, typically up to six or more depending on the machine size, with these wheels being qualified and stored directly on the machine. This capability is transformative for productivity.
Mr Rood explains: “With an ATC, outer diameter (OD), internal diameter (ID), and facing operations can all be completed in a single operation. This drastically reduces setup time, especially for small batch runs, as tooling up for popular jobs requires only a fixture and program change, not wheel changes and requalification of offsets etc.”
The benefits of the ATC are particularly evident in ID grinding. This often requires smaller wheels than those used for OD grinding. While typical horizontal universal grinders might offer only one ID wheel, limiting options for significant stock removal, the vertical grinder’s ATC can store multiple ID wheels. This allows for separate wheels dedicated to roughing and finishing operations.
Using a coarser grit wheel for roughing enables faster stock removal with less heat transfer, while a separate finishing wheel, used with reduced finish stock amounts, significantly increases its lifespan. This separation leads to perfectly sharp abrasives for finishing, reducing grinding forces, helping to minimise taper, and ultimately providing better process stability, part quality, and accuracy.
Made to measure
Vertical grinding machines offer a unique advantage in integrated part measuring. Unlike many horizontal machines, where probes are often used only for end-of-part flagging, vertical grinders can accurately measure internal and external diameters and faces with the same probe device. This device can also provide in-machine feedback for size correction.
“For larger parts, this integrated measuring capability is invaluable,” notes Mr Rood. “It avoids the labour-intensive process of removing heavy parts for manual measurement or attempting awkward measurements on the machine. Combined with the probe’s precision linear axis for multi-position measurement and calibration ring for thermal expansion correction, it virtually eliminates scrap and the need to rerun parts.”
Another significant benefit of vertical machines is improved workpiece rigidity and the effective use of gravity. The design of a vertical grinder offers significantly better face contact for workpiece mounting compared to horizontal machines. For instance, a vertical grinder with an 500mm part swing can offer 100% face contact up to 680mm, while a similar-sized horizontal machine might only provide around 250mm of face contact.
Furthermore, gravity works with the vertical machine, helping parts sit naturally against the jaw, EM chuck or fixture. This means less clamping force is needed, resulting in less part distortion and leading to better part roundness and accuracy, a benefit that becomes more pronounced with larger parts.
“Gravity is your friend in vertical grinding,” Mr Rood states. “Less clamping force means less distortion, which directly translates to better part quality.”
Easy automation
Automation is becoming increasingly important in manufacturing, and vertical machines are inherently well-suited for this. Most parts are naturally oriented for vertical machines, simplifying the integration of robots or pick-and-place units from bins or conveyors, often without requiring part reorientation. Easy access through the side of the machine enclosure facilitates loading devices.
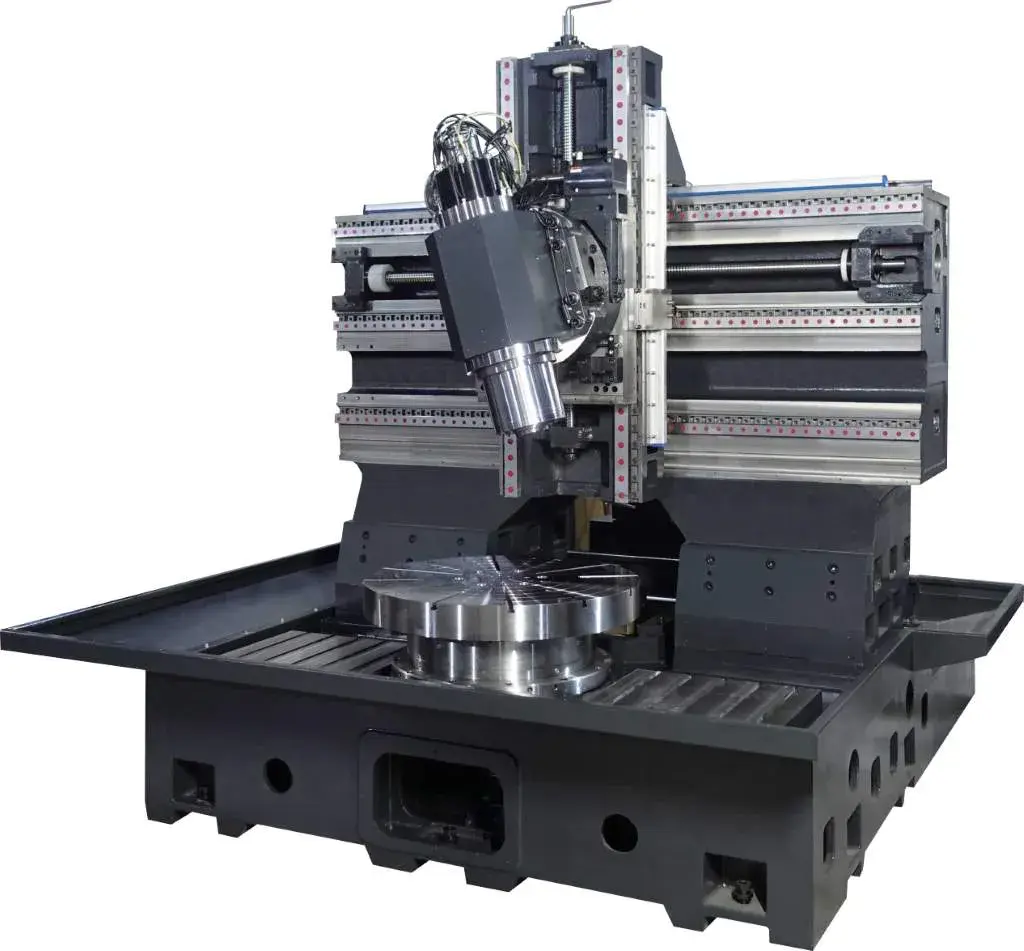
In terms of floor space, vertical grinding machines offer a considerable advantage. A horizontal universal machine designed for “between-centre” grinding, with a typical work head height and distance between centres, can have a large footprint. A comparable vertical grinder, even with a larger part swing diameter, can have a footprint that is nearly 50% less in width.
“Vertical machine design builds upward rather than outward,” concludes Mr Rood. “You get more part diameter capacity using half the floor space, optimising your workshop layout.”
For more information visit the RK International website.
RK International